A Look into Lapis Lazuli
Copyright no sections to be used without permission.
Lapis Lazuli an article by the renowned authority David Margulies
Lapis lazuli was described by Pliny the Elder as ‘a fragment of the starry vault of heaven’. It is, and always has been, the most exotic of semi-precious stones and pigments. The best quality blue stone is to be found high in the mountains at Sar-i-Sang, Badakhshan province, north eastern Afghanistan. To our knowledge the oldest use of the lapis lazuli from that source dates back 9,000 years in the form of beads found at Mehrgarh, in present day Pakistan. Lesser quality stone can be found in the same mountain range in today’s Tajikistan. Another source for the stone is in the region of Lake Baikal, Siberia. There are deposits in Chile, Canada, America, Angola and Italy.
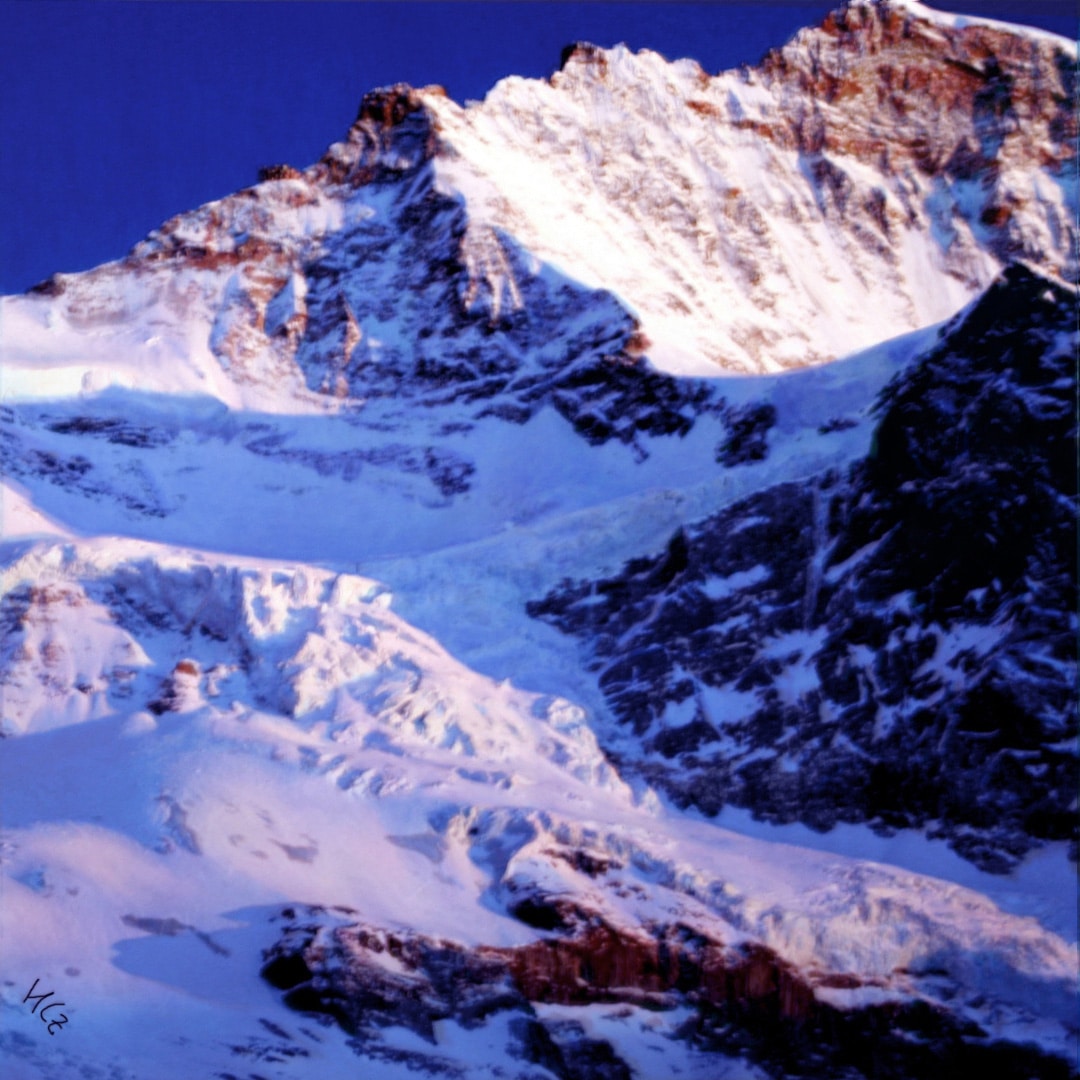
A Look into Lapis Lazuli
Copyright no sections to be used without permission.
Lapis Lazuli an article by the renowned authority David Margulies
Lapis lazuli was described by Pliny the Elder as ‘a fragment of the starry vault of heaven’. It is, and always has been, the most exotic of semi-precious stones and pigments. The best quality blue stone is to be found high in the mountains at Sar-i-Sang, Badakhshan province, north eastern Afghanistan. To our knowledge the oldest use of the lapis lazuli from that source dates back 9,000 years in the form of beads found at Mehrgarh, in present day Pakistan. Lesser quality stone can be found in the same mountain range in today’s Tajikistan. Another source for the stone is in the region of Lake Baikal, Siberia. There are deposits in Chile, Canada, America, Angola and Italy.
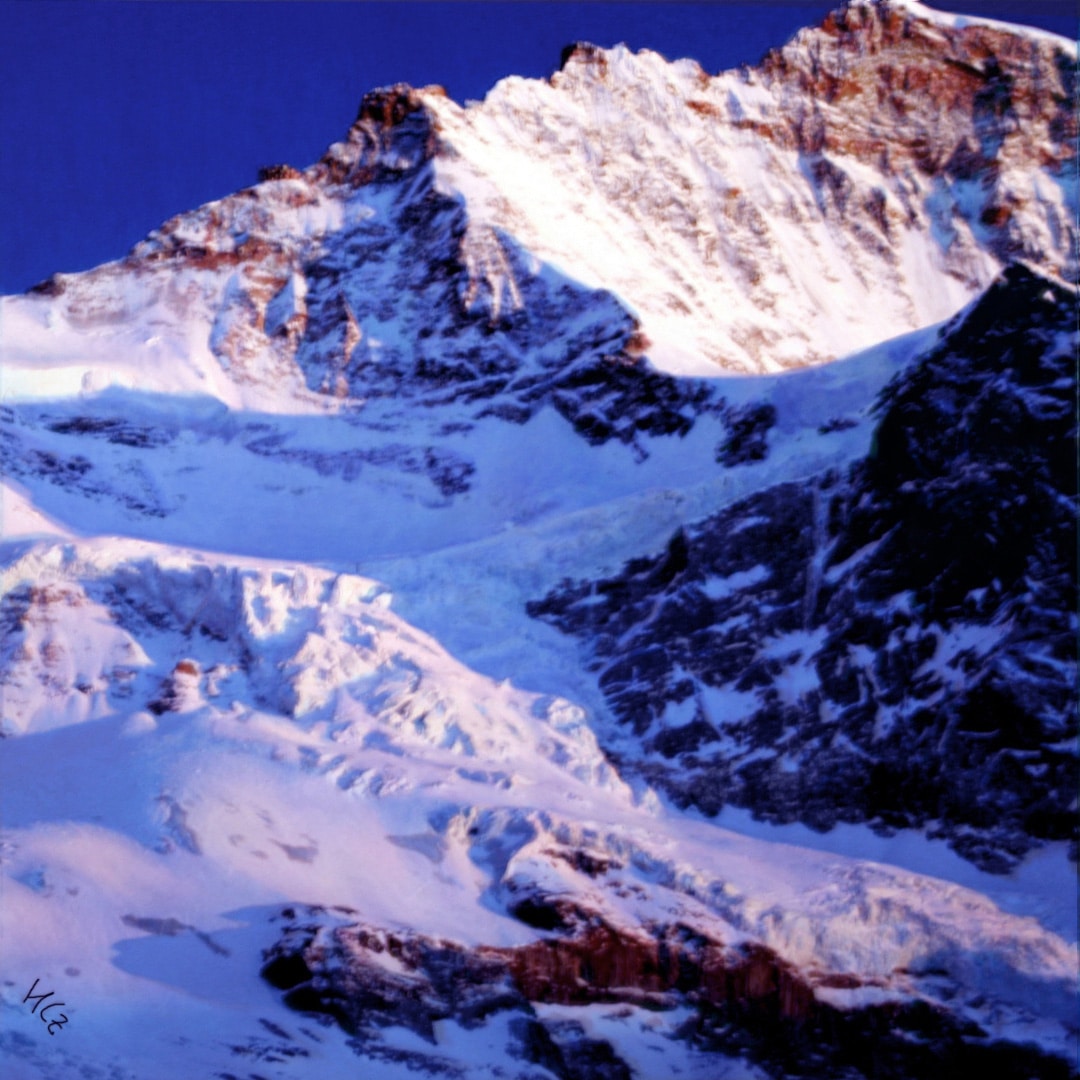
Much of the writings about the stone and the pigment are surrounded with myth and mistakes, much by transmitted error. The first myth is that the word lazuli is derived from the Persian, ‘lajward’. In fact we do not know where the word originated from. The Old Persian word is ‘kasakaina’, while Middle Persian was ‘Kasken’. The word did find itself transmitted into New Persian. A similar word, ‘lazaward’, was transmitted into Arabic and thence into Medieval Latin as ‘lazzulum’ or ‘azzurum’. The word was translated into French as ‘azur’, and into English as ‘azure’. The pigment that is obtained from the stone is known in English as ‘genuine ultramarine’. The term ‘genuine’ is to assist in differentiating it with the synthetically made French ultramarine. French ultramarine was so called because it was a Frenchman, Jean-Baptiste Guimet who won a prize in 1828, offered by the Societe d’Encouragement for developing a synthetic alternative to the mined ultramarine. Ironically, it was the French who named the Holy States, ‘Outremer’, (in parts of present-day Syria, Iraq and Lebanon) during the First Crusades of 1096 to 1099,. The Latin for outremer was ‘ultra marinus’, ’beyond the sea’. The name of the pigment thus became ‘ultramarine’ in English. It should be noted that the word ‘azure’ was also used to describe another blue pigment. To confuse matters further, the lapis mines in Afghanistan are still translated by Afghan writers as the ‘azure mines’. The earliest known use of the stone is as beads found in Mehrgarh, in present day Pakistan, dating back to 7,000B.C. The first known use of the pigment was on an Egyptian funerary artefact, circa 1580 to 1550 B.C. and though found in a lime plaster paint mix with red iron oxide on a wall painting in Greece in the 13th century B.C., it is clear that such early finds are rare. The earliest known use of the pigment in England has been analysed by Professor Robin Clark in a manuscript, later restored in 920A.D. The first major use of the pigment was in the Buddhist wall paintings of the Kizil and Dunhuang caves in present day China from around the 4th to the 6th centuries A.D. During the 15th and 16th Century, one can find the very highest quality ultramarine being used by artists from Northern Europe, extending to Asia. One of the finest examples of the use of ultramarine is in a painting of the Italian Renaissance, ‘Bacchus and Ariadne’ by Titian, 1521 to 1523, National Gallery, London. The Divan of the Sultan Husain Baiqara, circa 1490, executed in Herat is a fine example of ultramarine so often found in Islamic art of the same period.
Lapis lazuli is not one mineral but the name given to a collection of up to nine different minerals, some sharing the same elements. The main minerals are lazurite, hauynite, sodalite, noselite, calcite and pyrite. The specific mineral that bears the blue of the pigment is named lazurite. Lazurite comes in two forms, though both are crystals. One form is rock-like, while the other has an isometric crystal structure with the appearance of blue nuggets sitting on a matrix of white calcite crystals. It is the latter that geologists name as lazurite.
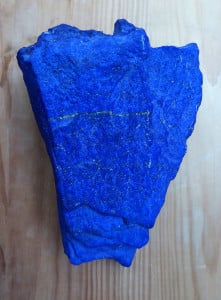
It is the quantity of sulphur radical anions trapped within the cubic holes in the lazurite lattice which determines the blue colouring. Even the chemical formulae for lazurite vary depending on location or even from seam to seam. Joyce Plesters, working at the Scientific Department of the National gallery, defined it as follows: 9Na, Ca) 8 (AlSiO4)6(SO4, S, Cl) 2 The main differences between synthetically produced French ultramarine and genuine ultramarine obtained from lapis lazuli are as follows: 1. The pigment particles of French ultramarine are very fine and uniform. 2. The crystals of French ultramarine are of a consistent blue colour. 3. Because French ultramarine crystals are smaller and more regular they diffuse light more evenly. 4. French ultramarine pigment has a strong electro-magnetic reaction, particularly visible if mixed into linseed oil. 5. Genuine ultramarine particles are irregular in size and the shape tends to be conchoidal, that is to say, shell-like. 6. The particles or fractures are more transparent in comparison with French ultramarine. This would explain the luminous quality of the reddish blue paint films of Renaissance, and post-Renaissance paintings. 7. Finally, the major characteristic of the crystal fractures of genuine ultramarine is that they are not uniformly blue. Examined under a microscope, the fractures can vary between those that possess a rich blue colouring, full of sulphur.
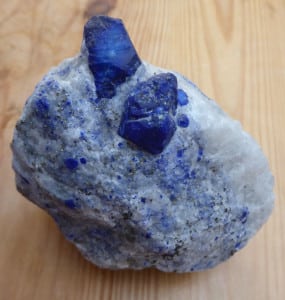
Others may appear to be less and less blue; while some will appear to have no blue colouring. There are three ways of preparing pigment from the solid mass. 1. Crushing, grinding, washing and levigating. 2. The ‘pastille’ method, as exemplified by the recipe of Cennino Cennini, Italian, 15th Century. 3. The froth floatation method; the most common commercial process in use today. Many commentators throughout the past few hundred years have repeated the axiom that, however blue (or pure) the mass, it will not be sufficient to rely on grinding and washing in order to achieve the best results. ‘As Plesters [Joyce Plesters, Scientific Dept. National gallery, London, 1949-1987] has noted, unless the lapis lazuli from which the pigment is prepared is of exceptional quality, simply grinding and washing produces only a greyish blue powder’. Pigment Compendium, A Dictionary of Historical Pigments’. Contributors: Nicholas Eastaugh, Valentine Walsh, Tracy Chapman, Ruth Siddall. Publ. Elsevier Butterworth Heinemann, 2004. Page 219. “You can’t just take lapis lazuli, however good the quality of the colour and just grind it up and mix it with a paint medium to make a very satisfactory pigment. You actually have to extract the pigment from the mixture of minerals that constitute lapis lazuli.” Ashok Roy, Director of Scientific Research. Director of Collections. National Gallery, London. ‘The Story of Blue’. Nature Video. YouTube, published 14th August, 2014.
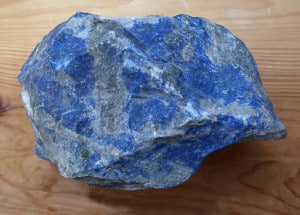
Of course, one, if not the major issue, is the type and quality of the mass that one uses in the production of the pigment. Lapis lazuli from Chile may typically contain a very high percentage of impurities. It is believed that Cennino Cennini wrote ‘Il Libro Dell’Arte’, the most famous of artists’ treatises. Unfortunately there are no original texts in existence. We only have a copy of a copy, dated 1437. He wrote: ‘ And if you want to recognise a good stone, take that which you can see has a greater blue-coloured content, although it all has something like ash mixed in. That which contains less of the ash colour, that is better.’ Page90. Lara Broecke translation. Archetype Publications. 2015. Broecke writes in her foot note: ‘The ash coloured material to which Cennino refers consists of calcite and pyrites (and often other materials), which are present alongside the blue lazurite in lapis lazuli.’ Chapter 62. Page 90. It cannot be emphasized enough. Cennino was referring to the impurities that could be seen, the calcite and pyrites. He was not referring to what he could not see. It should therefore be considered that all of the sources that state that grinding solely will produce a greyish blue powder are in fact referring to lapis with a degree of calcite and pyrites left in the mix. However, many of the sources do emphasize that the choice of the stone in the first place will influence the quality of the pigment produced from it. It should also be pointed out that it is quite easy to pick out much of the calcite as the grinding proceeds. It is also possible to wash out much of the pyrites as it is broken off the lazurite particles.
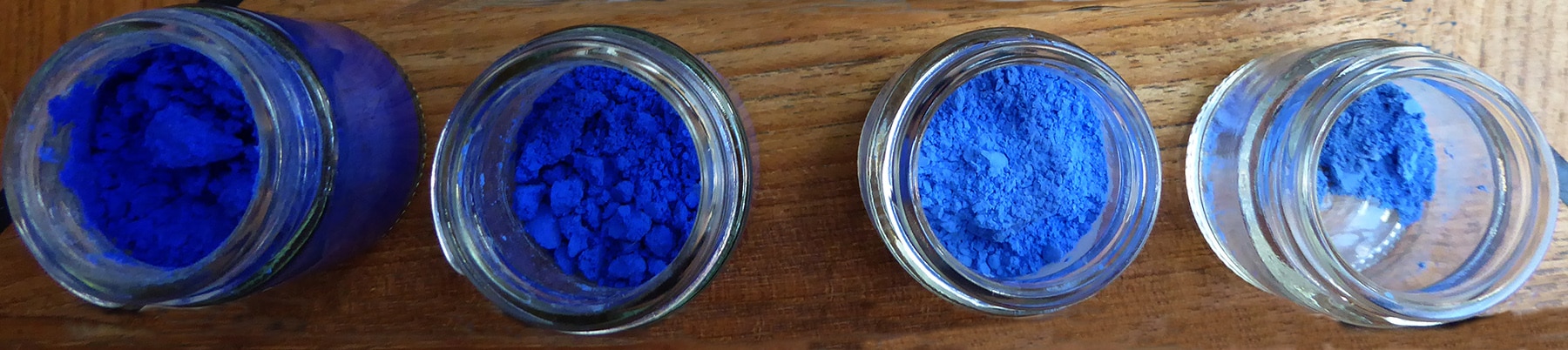
In professor Yves Porter’s monograph, ‘Painters, Paintings, and Books’, he quotes Persian sources under the heading of ‘Techniques for Washing Lapis’. He states: ‘Several methods more or less sophisticated are suggested in various texts. Indeed crushed and unwashed lapis gives a bluish-grey colour, which is very far from ultramarine. The long and delicate process of washing lapis kept a whole body of professionals (lajvard-shuyan) occupied within the workshops.’ It would be correct to state that simply grinding lapis lazuli consisting of much calcite and pyrites, would produce greyish-blue powder. However, even those who recommend the pastille method clearly state that one should commence with the best quality lapis lazuli with the highest blue content (lazurite) and very least calcite and or pyrites. The second suggested method of producing the best quality blue pigment is through the ‘pastille’ method, first known reference is the method ascribed to Geber, the 8th century Arab alchemist. Since that time there were many authors who described a ‘pastille’ method. The most famous and most detailed recipe could be found in Cennino Cennini’s ‘Il Libro Dell’Arte’. The recipe refers to mixing the ground lapis lazuli with pine resin, mastic, fresh wax into a ball, then covered with linseed oil. This was to be left for a number of days and then kneaded in a warm bath of lye. The best deepest lazurite is meant to fall out of the ball into the lye, which is then poured off leaving the pigment to be collected. The kneading process would be done in a new bath of lye and yet more pigment would fall out into the lye. This would be deemed to be the second grade of lazurite pigment. This process would continue with another clean bath of lye yielding yet a further lower grade of blue, until the final yield which would be known as ultramarine ‘ash’ because of the greyish colouring. Cennini ends his section on the purification of the ultramarine by humorously advising: ‘ And know that it is more the business of lovely young girls than men to make it because they stay put in the house all the time and have more delicate hands; watch out for old women though.’ Lara Broecke translation. This method can only be confirmed as effective if it can be repeated. Unfortunately, there are a number of professionals who have found that this method produces extremely inconsistent results. The other issue with this method can best be illustrated by the most elegant experiments published. Following the closest recreation of Cennini’s recipe the results were as follows: Of a total of 50g of lapis lazuli mass, all that was yielded of Grade 1 quality was 0.45g- representing 0.9% of the total. Grade 2 yielded 0.45g – representing 0.9% of the total.
Grade 3 yielded 0.47g – representing 0.94% of the total.
Grade 4 yielded 0.22g – representing 0.44% of the total.
Of the 50 g, the method yielded 1.59g of pigment– representing 3.18% of the total.
This means that 48.41 grams would remain lost in the pastille, a shocking loss of 96.82%. This would strongly suggest that this method would not be commercially viable. The third way of producing ultramarine from the ground lapis lazuli is through the froth ‘floatation’ method. The intention of this method is to be able to create an economically viable way to separate the lazurite particles from the impurities that are found in the mass. The mass (rock) is ground and then placed in a bath of water which can be heated, aerated and agitated, creating bubbles. The procedure is carried out in three stages.
1. The removal of iron pyrites.
2. The removal of calcites.
3. The removal of mica, quartz and other silicates.
The process is under patent pending. Much of the details of the alkali reagents, and more surprisingly, acid reagent, added at the different stages, are still a matter of trade secret. These reagents consist of a hydrophilic and a hydrophobic group called ‘foamers’. In the first stage the pyrites cling to the surface of the bubbles and are then skimmed off and away.
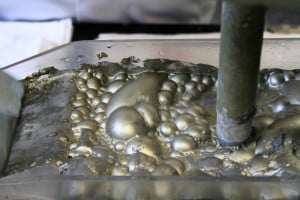
Using different reagents the carbonates are then skimmed off. In the third stage an acid reagent is rapidly introduced to decompose the poly-sulphates. An alkali is added to neutralise the acid before it can damage the lazurite particles. The water plus the reagents are washed out of the container leaving the lazurite lying at the bottom of the container. The lazurite particles are washed out thoroughly to remove any traces of the reagents and left to dry.
Earlier it was mentioned that the greyish appearance of the pigment described by Cennini et al was because of the visible impurities such as calcite and pyrites. There is another reason why the powder may have a greyish blue appearance. With the use of a petrographic microscope It is possible to observe pigment structures invisible to the naked eye which may also explain why the powder can appears greyish blue.
When examining the pigment particles microscopically, from all three of the above-mentioned production methods, it is clear that they share one characteristic in common. The conchoidal fractures contain different amounts of the sulphur anions.
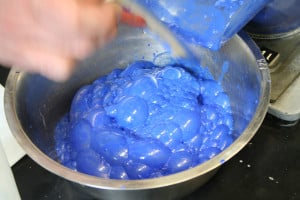
There are those that will contain a large quantity of sulphur, and are of the richest blue. There are those fractures with less sulphur and will appear to be of a paler blue, and there will be fractures that have no colour. The presence of partially blue and transparent particles of genuine ultramarine will dictate whether the pigment, in dry form, appears more or less blue to greyish blue. Even if the lazurite mass appears to be pure blue, with no calcite and pyrite present, it will contain varying grades of chroma, depending on the source (from which mine and from which country). The quality and chroma will even vary from seam to seam in the same mine.
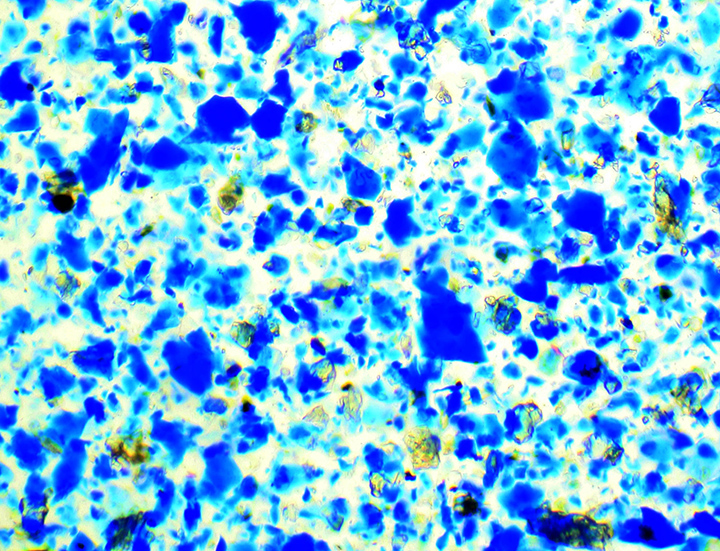
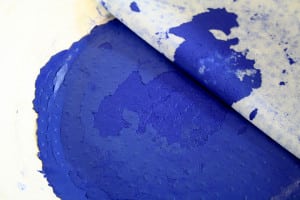
The finest blue pigment comes from a rock which is dark blue, almost blackish purple with the least amount of impurities. And even then, one cannot anticipate the quality of the pigment before the rock or crystal is broken up and ground.
David Margulies
London 2015
Copyright no sections to be used without permission.
Much of the writings about the stone and the pigment are surrounded with myth and mistakes, much by transmitted error. The first myth is that the word lazuli is derived from the Persian, ‘lajward’. In fact we do not know where the word originated from. The Old Persian word is ‘kasakaina’, while Middle Persian was ‘Kasken’. The word did find itself transmitted into New Persian. A similar word, ‘lazaward’, was transmitted into Arabic and thence into Medieval Latin as ‘lazzulum’ or ‘azzurum’. The word was translated into French as ‘azur’, and into English as ‘azure’. The pigment that is obtained from the stone is known in English as ‘genuine ultramarine’. The term ‘genuine’ is to assist in differentiating it with the synthetically made French ultramarine. French ultramarine was so called because it was a Frenchman, Jean-Baptiste Guimet who won a prize in 1828, offered by the Societe d’Encouragement for developing a synthetic alternative to the mined ultramarine. Ironically, it was the French who named the Holy States, ‘Outremer’, (in parts of present-day Syria, Iraq and Lebanon) during the First Crusades of 1096 to 1099,. The Latin for outremer was ‘ultra marinus’, ’beyond the sea’. The name of the pigment thus became ‘ultramarine’ in English. It should be noted that the word ‘azure’ was also used to describe another blue pigment. To confuse matters further, the lapis mines in Afghanistan are still translated by Afghan writers as the ‘azure mines’. The earliest known use of the stone is as beads found in Mehrgarh, in present day Pakistan, dating back to 7,000B.C. The first known use of the pigment was on an Egyptian funerary artefact, circa 1580 to 1550 B.C. and though found in a lime plaster paint mix with red iron oxide on a wall painting in Greece in the 13th century B.C., it is clear that such early finds are rare. The earliest known use of the pigment in England has been analysed by Professor Robin Clark in a manuscript, later restored in 920A.D. The first major use of the pigment was in the Buddhist wall paintings of the Kizil and Dunhuang caves in present day China from around the 4th to the 6th centuries A.D. During the 15th and 16th Century, one can find the very highest quality ultramarine being used by artists from Northern Europe, extending to Asia. One of the finest examples of the use of ultramarine is in a painting of the Italian Renaissance, ‘Bacchus and Ariadne’ by Titian, 1521 to 1523, National Gallery, London. The Divan of the Sultan Husain Baiqara, circa 1490, executed in Herat is a fine example of ultramarine so often found in Islamic art of the same period.
Lapis lazuli is not one mineral but the name given to a collection of up to nine different minerals, some sharing the same elements. The main minerals are lazurite, hauynite, sodalite, noselite, calcite and pyrite. The specific mineral that bears the blue of the pigment is named lazurite. Lazurite comes in two forms, though both are crystals. One form is rock-like, while the other has an isometric crystal structure with the appearance of blue nuggets sitting on a matrix of white calcite crystals. It is the latter that geologists name as lazurite.
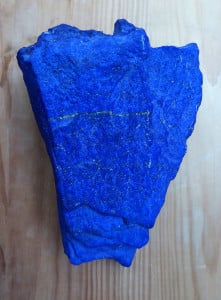
It is the quantity of sulphur radical anions trapped within the cubic holes in the lazurite lattice which determines the blue colouring. Even the chemical formulae for lazurite vary depending on location or even from seam to seam. Joyce Plesters, working at the Scientific Department of the National gallery, defined it as follows: 9Na, Ca) 8 (AlSiO4)6(SO4, S, Cl) 2 The main differences between synthetically produced French ultramarine and genuine ultramarine obtained from lapis lazuli are as follows: 1. The pigment particles of French ultramarine are very fine and uniform. 2. The crystals of French ultramarine are of a consistent blue colour. 3. Because French ultramarine crystals are smaller and more regular they diffuse light more evenly. 4. French ultramarine pigment has a strong electro-magnetic reaction, particularly visible if mixed into linseed oil. 5. Genuine ultramarine particles are irregular in size and the shape tends to be conchoidal, that is to say, shell-like. 6. The particles or fractures are more transparent in comparison with French ultramarine. This would explain the luminous quality of the reddish blue paint films of Renaissance, and post-Renaissance paintings. 7. Finally, the major characteristic of the crystal fractures of genuine ultramarine is that they are not uniformly blue. Examined under a microscope, the fractures can vary between those that possess a rich blue colouring, full of sulphur.
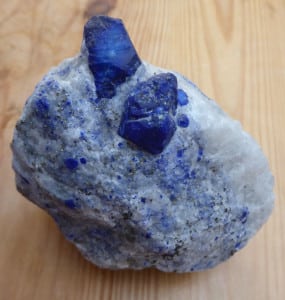
Others may appear to be less and less blue; while some will appear to have no blue colouring. There are three ways of preparing pigment from the solid mass. 1. Crushing, grinding, washing and levigating. 2. The ‘pastille’ method, as exemplified by the recipe of Cennino Cennini, Italian, 15th Century. 3. The froth floatation method; the most common commercial process in use today. Many commentators throughout the past few hundred years have repeated the axiom that, however blue (or pure) the mass, it will not be sufficient to rely on grinding and washing in order to achieve the best results. ‘As Plesters [Joyce Plesters, Scientific Dept. National gallery, London, 1949-1987] has noted, unless the lapis lazuli from which the pigment is prepared is of exceptional quality, simply grinding and washing produces only a greyish blue powder’. Pigment Compendium, A Dictionary of Historical Pigments’. Contributors: Nicholas Eastaugh, Valentine Walsh, Tracy Chapman, Ruth Siddall. Publ. Elsevier Butterworth Heinemann, 2004. Page 219. “You can’t just take lapis lazuli, however good the quality of the colour and just grind it up and mix it with a paint medium to make a very satisfactory pigment. You actually have to extract the pigment from the mixture of minerals that constitute lapis lazuli.” Ashok Roy, Director of Scientific Research. Director of Collections. National Gallery, London. ‘The Story of Blue’. Nature Video. YouTube, published 14th August, 2014.
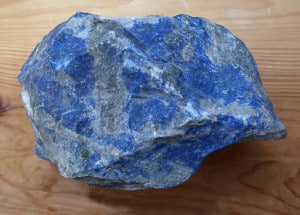
Of course, one, if not the major issue, is the type and quality of the mass that one uses in the production of the pigment. Lapis lazuli from Chile may typically contain a very high percentage of impurities. It is believed that Cennino Cennini wrote ‘Il Libro Dell’Arte’, the most famous of artists’ treatises. Unfortunately there are no original texts in existence. We only have a copy of a copy, dated 1437. He wrote: ‘ And if you want to recognise a good stone, take that which you can see has a greater blue-coloured content, although it all has something like ash mixed in. That which contains less of the ash colour, that is better.’ Page90. Lara Broecke translation. Archetype Publications. 2015. Broecke writes in her foot note: ‘The ash coloured material to which Cennino refers consists of calcite and pyrites (and often other materials), which are present alongside the blue lazurite in lapis lazuli.’ Chapter 62. Page 90. It cannot be emphasized enough. Cennino was referring to the impurities that could be seen, the calcite and pyrites. He was not referring to what he could not see. It should therefore be considered that all of the sources that state that grinding solely will produce a greyish blue powder are in fact referring to lapis with a degree of calcite and pyrites left in the mix. However, many of the sources do emphasize that the choice of the stone in the first place will influence the quality of the pigment produced from it. It should also be pointed out that it is quite easy to pick out much of the calcite as the grinding proceeds. It is also possible to wash out much of the pyrites as it is broken off the lazurite particles.
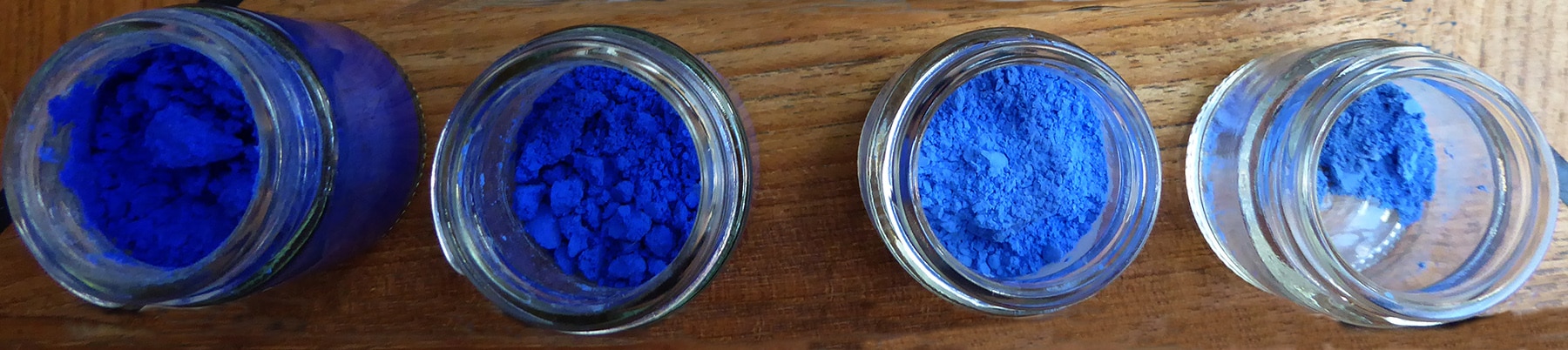
In professor Yves Porter’s monograph, ‘Painters, Paintings, and Books’, he quotes Persian sources under the heading of ‘Techniques for Washing Lapis’. He states: ‘Several methods more or less sophisticated are suggested in various texts. Indeed crushed and unwashed lapis gives a bluish-grey colour, which is very far from ultramarine. The long and delicate process of washing lapis kept a whole body of professionals (lajvard-shuyan) occupied within the workshops.’ It would be correct to state that simply grinding lapis lazuli consisting of much calcite and pyrites, would produce greyish-blue powder. However, even those who recommend the pastille method clearly state that one should commence with the best quality lapis lazuli with the highest blue content (lazurite) and very least calcite and or pyrites. The second suggested method of producing the best quality blue pigment is through the ‘pastille’ method, first known reference is the method ascribed to Geber, the 8th century Arab alchemist. Since that time there were many authors who described a ‘pastille’ method. The most famous and most detailed recipe could be found in Cennino Cennini’s ‘Il Libro Dell’Arte’. The recipe refers to mixing the ground lapis lazuli with pine resin, mastic, fresh wax into a ball, then covered with linseed oil. This was to be left for a number of days and then kneaded in a warm bath of lye. The best deepest lazurite is meant to fall out of the ball into the lye, which is then poured off leaving the pigment to be collected. The kneading process would be done in a new bath of lye and yet more pigment would fall out into the lye. This would be deemed to be the second grade of lazurite pigment. This process would continue with another clean bath of lye yielding yet a further lower grade of blue, until the final yield which would be known as ultramarine ‘ash’ because of the greyish colouring. Cennini ends his section on the purification of the ultramarine by humorously advising: ‘ And know that it is more the business of lovely young girls than men to make it because they stay put in the house all the time and have more delicate hands; watch out for old women though.’ Lara Broecke translation. This method can only be confirmed as effective if it can be repeated. Unfortunately, there are a number of professionals who have found that this method produces extremely inconsistent results. The other issue with this method can best be illustrated by the most elegant experiments published. Following the closest recreation of Cennini’s recipe the results were as follows: Of a total of 50g of lapis lazuli mass, all that was yielded of Grade 1 quality was 0.45g- representing 0.9% of the total. Grade 2 yielded 0.45g – representing 0.9% of the total.
Grade 3 yielded 0.47g – representing 0.94% of the total.
Grade 4 yielded 0.22g – representing 0.44% of the total.
Of the 50 g, the method yielded 1.59g of pigment– representing 3.18% of the total.
This means that 48.41 grams would remain lost in the pastille, a shocking loss of 96.82%. This would strongly suggest that this method would not be commercially viable. The third way of producing ultramarine from the ground lapis lazuli is through the froth ‘floatation’ method. The intention of this method is to be able to create an economically viable way to separate the lazurite particles from the impurities that are found in the mass. The mass (rock) is ground and then placed in a bath of water which can be heated, aerated and agitated, creating bubbles. The procedure is carried out in three stages.
1. The removal of iron pyrites.
2. The removal of calcites.
3. The removal of mica, quartz and other silicates.
The process is under patent pending. Much of the details of the alkali reagents, and more surprisingly, acid reagent, added at the different stages, are still a matter of trade secret. These reagents consist of a hydrophilic and a hydrophobic group called ‘foamers’. In the first stage the pyrites cling to the surface of the bubbles and are then skimmed off and away.
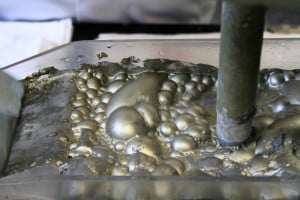
Using different reagents the carbonates are then skimmed off. In the third stage an acid reagent is rapidly introduced to decompose the poly-sulphates. An alkali is added to neutralise the acid before it can damage the lazurite particles. The water plus the reagents are washed out of the container leaving the lazurite lying at the bottom of the container. The lazurite particles are washed out thoroughly to remove any traces of the reagents and left to dry.
Earlier it was mentioned that the greyish appearance of the pigment described by Cennini et al was because of the visible impurities such as calcite and pyrites. There is another reason why the powder may have a greyish blue appearance. With the use of a petrographic microscope It is possible to observe pigment structures invisible to the naked eye which may also explain why the powder can appears greyish blue.
When examining the pigment particles microscopically, from all three of the above-mentioned production methods, it is clear that they share one characteristic in common. The conchoidal fractures contain different amounts of the sulphur anions.
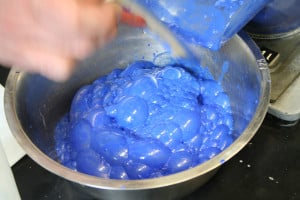
There are those that will contain a large quantity of sulphur, and are of the richest blue. There are those fractures with less sulphur and will appear to be of a paler blue, and there will be fractures that have no colour. The presence of partially blue and transparent particles of genuine ultramarine will dictate whether the pigment, in dry form, appears more or less blue to greyish blue. Even if the lazurite mass appears to be pure blue, with no calcite and pyrite present, it will contain varying grades of chroma, depending on the source (from which mine and from which country). The quality and chroma will even vary from seam to seam in the same mine.
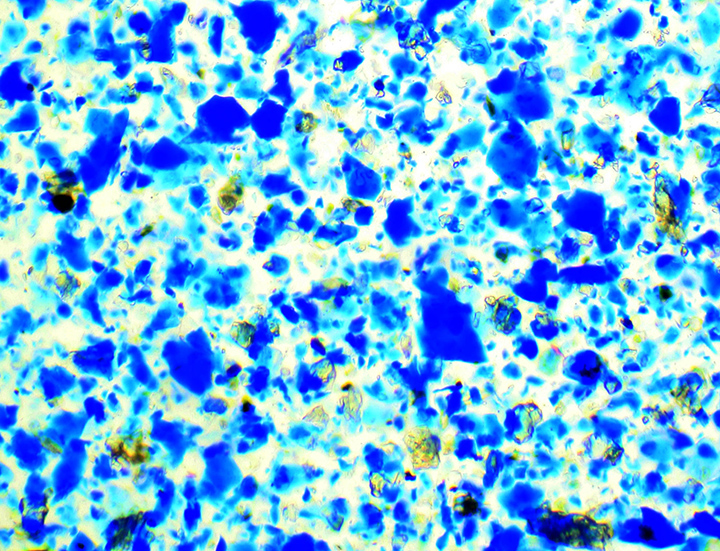
Fig.8. Froth flotation method. Mag.X10. Grade 1 lazurite. Note the remaining impurities.
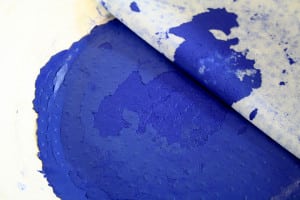
Fig.7. Washed and blotted ultramarine after the froth flotation method.
The finest blue pigment comes from a rock which is dark blue, almost blackish purple with the least amount of impurities. And even then, one cannot anticipate the quality of the pigment before the rock or crystal is broken up and ground.
David Margulies
London 2015
Copyright no sections to be used without permission.